FABBRICA ITALIANA LAMIERE
PRODUCTION PROCESS
WHAT IS IT?
HOT ROLLING
Rolling is the mechanical process used to reduce the least significant measurement in a sheet, usually the thickness.
This process is carried out by means of opposing cylinders which, rotating, impress the desired shape on the material.
In particular, the hot rolling of FIL, is a high temperature mechanical working process performed to reduce the thickness of the sheet metal.
The sheets resulting from hot rolling processes are also known as “train sheet” and are generally considered industrial semi-finished products to be processed subsequently by cold rolling or to be used for heavy carpentry.
The products that can be obtained by rolling can be divided into three main product families:
- flat products, consisting of strips, sheets and wide plates
- long products, consisting of sections, bars and rounds
- seamless pipes
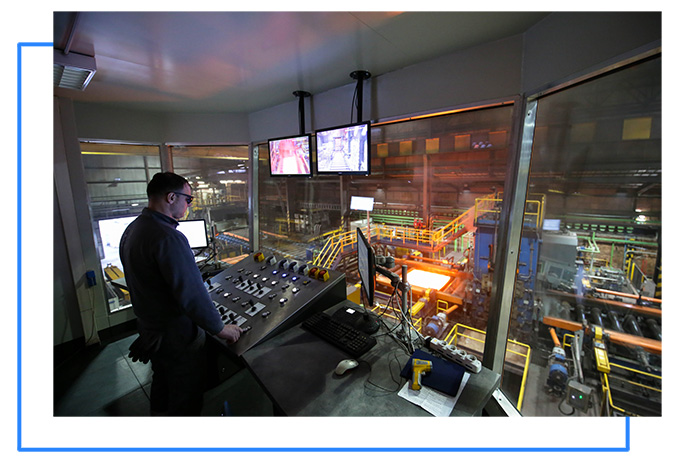
The semi-finished products are placed in continuous operation furnaces heated with oxyfuel burners, to be brought to a temperature of 1200-1300 °C, and then sent to a rolling mill, i.e. to a plant consisting of one or more rolling cages, where with subsequent deformations the section with the required shape is produced. The rolling mills are equipped with roller conducts, which facilitate the movement of the semi-finished product between one cage and another (tilters, manipulators, draggers, etc.), between shears, saws or piers for hot cutting, and finally cooling plates or carpets.
The laminate is then collected, cut to size and packaged.
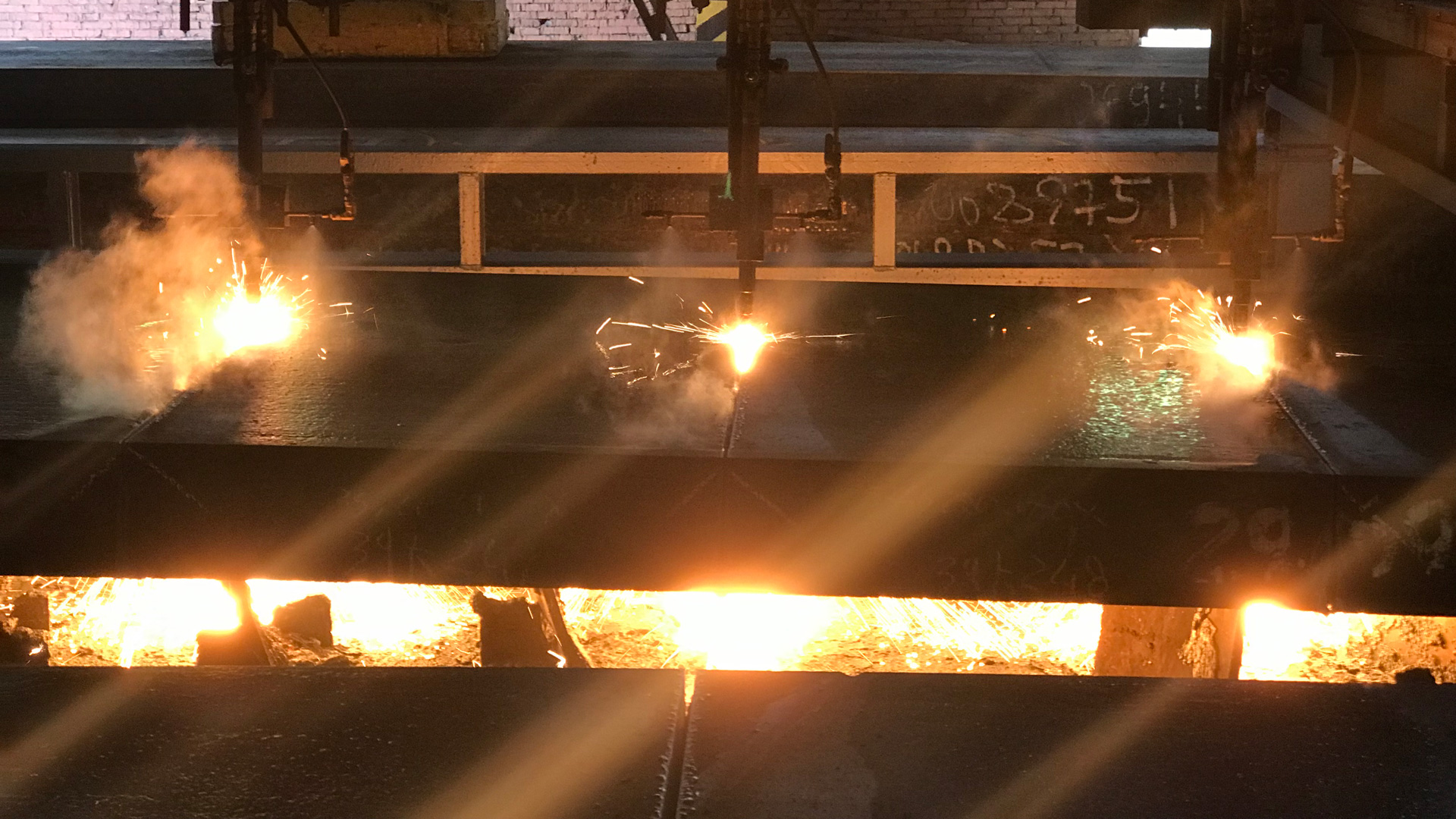
BRAMME
STORAGE AND CUTTING
FABBRICA ITALIANA LAMIERE produces hot metal sheets intended for use in metal carpentry, following a very precise process:
the semi-finished products produced by the steel industry, i.e. carbon steel slabs, are cut by oxyfuel cutting according to the geometric size of the sheet metal required.
PRE-HEAT
OVEN
Subsequently, the slabs are preheated in preheating ovens.
In 2012 the latest generation reheating oven was built by Bendotti, a leading company in the sector.
The purposes of pre-heating the semi-finished products fed to the rolling are:
- facilitate the operation of deformation of the material;
- ensure that hot rolling takes place at the required process temperatures in all its stages;
- allow the solubilization, where necessary, of specific elements within the sheet metal matrix.
The energy needed for heating is normally supplied by the combustion of natural gas.
Pusher ovens: each piece introduced pushes the previous ones forward, so that as a cold semi-finished product enters the oven a hot semi-finished product exits on the opposite side.

PROCESS OF
DESCALING
During heating inside the furnaces, flakes are formed on the surface of the material which are essentially composed of iron oxides. These flakes must be removed to prevent them from leaving scars on the surface of the material. The flakes can be removed by mechanical breakage with a slight lamination or by spraying water at high pressure on the surface of the material.
Descaling can be carried out not only at the time of entering the rolling mill train, and therefore at the start of rolling, but also at other times. In this case the purpose of the descaling is to remove the secondary flake, i.e. the one formed during the various passages under the rolling rollers.
PROCESS OF
HOT ROLLING
Lamination is a plastic deformation process, which is carried out by means of the compression of the semi-finished product between two cylinders rotating in the opposite direction, which make it advance by friction, reducing its section and, if the cylinders are molded, making it assume the desired profile.
The tools used to transmit the pressures necessary to deform the material are normally cylindrical in shape, rotating around their axis, and are called rolling cylinders.
The cylinders are kept in working position inside a cage, consisting of a sturdy metal frame that provides two dividing pillars supporting the cylinders, moved by the transmission components that transmit the movement of electric motors and the drives for adjusting the distance between the cylinders. In the most recent configurations, two shafts are mounted on a single mast and rolling rings are inserted on these rotating supports, simplifying all the problems related to tooling and restoring the deformation machine.
The metal is deformed through the pressure of the rollers against the plate surface, which causes a tensional state of compression and a consequent reduction in height. This reduction, due to the constancy of the volume, in turn generates a widening and lengthening of the semi-finished product at every step.
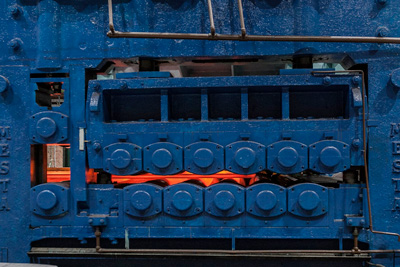
PROCESS OF
FLATTENING, LETTERING AND MARKING
In this phase the sheets are straightened by successive passages under the rollers of the levelling machine.
After straightening some of them are headed by cutting the head and tail of the sheet metal by means of two independent portals equipped with oxycutting torches.
From the letterhead phase, waste consisting of scrap metal is produced, which is also recycled.
STORAGE
FINISHED PRODUCT WAREHOUSE
Train, laser, ped and naval plates are stored in the rolling mill shed waiting for cooling to be completed and then sent to their destination.
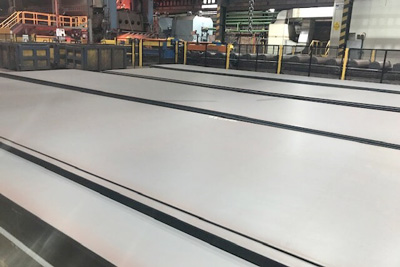